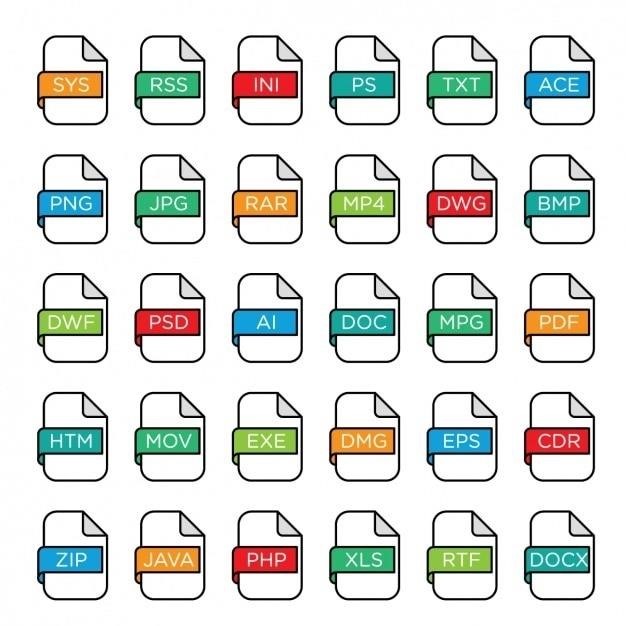
Geometric Dimensioning and Tolerancing (GD&T) employs symbols on engineering drawings to convey precision requirements from designers to manufacturers. These symbols define tolerances for size‚ form‚ orientation‚ and location of part features‚ ensuring accurate and consistent production. GD&T improves communication and reduces manufacturing errors.
Understanding Geometric Dimensioning and Tolerancing
Geometric Dimensioning and Tolerancing (GD&T) is a system for specifying tolerances on engineering drawings that goes beyond simple plus/minus tolerances. Instead of relying solely on numerical dimensions‚ GD&T utilizes symbols and a standardized language to define the permissible variations in a part’s geometry. This includes aspects like form (straightness‚ flatness‚ circularity‚ cylindricity)‚ orientation (parallelism‚ perpendicularity‚ angularity)‚ location (position‚ concentricity‚ symmetry)‚ and runout (circular runout‚ total runout). The system ensures that the manufactured part meets the required functional specifications‚ regardless of minor variations in dimensions.
GD&T is crucial because it allows for more precise control over critical features. This is especially important in applications where the functionality of a part depends on its precise geometry‚ such as in aerospace‚ automotive‚ and medical device manufacturing. Traditional dimensioning methods often lead to ambiguity and potential misinterpretations‚ whereas GD&T provides a clear and unambiguous way to communicate design intent.
By using GD&T symbols‚ designers can specify the acceptable variations in a part’s geometry‚ ensuring that the manufactured part meets the required functional specifications. This leads to improved product quality and reduced manufacturing costs.
The Importance of GD&T in Engineering Drawings
Incorporating GD&T into engineering drawings significantly enhances communication and precision throughout the manufacturing process. Traditional dimensioning methods often fall short in explicitly defining the acceptable variations in a part’s geometric features‚ potentially leading to misinterpretations and manufacturing defects. GD&T‚ however‚ provides a standardized and unambiguous language for specifying tolerances‚ minimizing ambiguity and ensuring that the final product conforms to the designer’s intent.
The use of GD&T symbols on drawings clarifies the permissible variations in form‚ orientation‚ location‚ and runout‚ which are crucial for functionality and interchangeability. This leads to improved product quality‚ reduced rework‚ and minimized manufacturing costs. Furthermore‚ GD&T facilitates better collaboration between designers and manufacturers‚ as both parties share a common understanding of the required geometric tolerances. This is especially critical in complex assemblies where the proper functioning of the entire system relies on the precise dimensions and geometry of individual components. Clear communication through GD&T promotes efficiency and reduces the likelihood of costly errors.
Adopting GD&T best practices results in more robust designs and more reliable manufacturing processes. It’s an investment in quality and precision.
Key GD&T Symbols and Their Meanings
This section details the core GD&T symbols‚ crucial for understanding engineering drawings. Each symbol represents specific geometric tolerances‚ ensuring precise manufacturing. A comprehensive understanding is vital for accurate interpretation and application.
Symbols for Form Tolerances
Form tolerances in GD&T define the allowable deviations from perfect geometric shapes. These deviations are crucial for ensuring proper functionality and interchangeability of parts. Key symbols include straightness‚ flatness‚ circularity (roundness)‚ and cylindricity. Straightness controls how much a line or axis can deviate from a perfectly straight line. Flatness dictates the allowable deviation of a surface from a perfectly flat plane. Circularity‚ also known as roundness‚ specifies the allowable variation in the diameter of a circle. Cylindricity defines the permissible deviation of a cylindrical surface from a perfect cylinder. Each symbol is accompanied by a tolerance zone‚ which represents the acceptable range of variation.
The application of these symbols ensures that manufactured parts conform to the intended geometric shapes within specified limits. Incorrect interpretation can lead to misalignment‚ improper fit‚ and functional failures. Therefore‚ understanding these form tolerance symbols is crucial for designers and manufacturers to ensure quality control and product performance.
Symbols for Orientation Tolerances
Orientation tolerances in GD&T specify the permissible angular deviations of features relative to a datum reference frame. These tolerances are critical for ensuring the proper alignment and assembly of parts. Key symbols include angularity‚ parallelism‚ and perpendicularity. Angularity controls the allowable deviation of a feature’s axis from a datum plane or axis at an angle other than 90 degrees. Parallelism defines the acceptable deviation of a feature from being parallel to a datum plane or axis. Perpendicularity specifies the allowed deviation of a feature from being perpendicular (90 degrees) to a datum plane or axis.
Each orientation tolerance symbol is associated with a tolerance zone that represents the allowable angular variation. The selection of the appropriate datum reference is crucial for defining the orientation tolerance. Incorrect datum selection can lead to inaccurate tolerance control and potential assembly issues. Proper understanding and application of these symbols are essential for achieving precise alignment and functionality in mechanical assemblies. These symbols are fundamental to ensuring the correct relative positioning of features within a component or assembly.
Symbols for Location Tolerances
Location tolerances in GD&T define the permissible positional variations of features relative to a datum reference frame. These tolerances are crucial for ensuring the proper fit and function of parts within an assembly. Key symbols include position‚ concentricity‚ and circularity. Position controls the allowable deviation of a feature’s location from its ideal position‚ defined by the datum reference. Concentricity specifies the permissible deviation of the axis of a feature from the axis of a datum feature. Circularity describes the roundness of a feature and is often used in conjunction with other tolerances to fully define its geometry.
Each location tolerance symbol is accompanied by a tolerance zone that represents the allowable positional variation. The size and shape of the tolerance zone depend on the specific tolerance and the datum reference used. The selection of the appropriate datum reference is paramount for defining the location tolerance accurately. Incorrect datum selection can lead to inaccurate tolerance control and potential assembly problems. Accurate application of these symbols is essential for achieving the desired fit and function of parts in mechanical assemblies. They are crucial for ensuring the correct spatial relationship between features within a component or assembly.
Advanced GD&T Concepts
Beyond basic symbols‚ advanced GD&T delves into datum references‚ feature control frames‚ and the crucial Rules 1 and 2. Mastering these concepts is vital for precise part definition and manufacturing. These rules govern tolerance application and interpretation.
Datum References and Feature Control Frames
Datum references are fundamental to GD&T‚ providing stable bases for measurements. They are typically established from specific features on a part‚ such as a plane‚ surface‚ or axis. These datums are denoted by uppercase letters (A‚ B‚ C‚ etc.) and serve as the reference points for controlling the location and orientation of other features. A datum feature is a physical element of the part selected to define a datum. The selection of appropriate datums is crucial for ensuring proper part functionality and interchangeability. Incorrect datum selection can lead to misinterpretations of tolerances and ultimately‚ manufacturing defects.
Feature Control Frames (FCFs) are rectangular boxes containing the geometric characteristic symbol‚ tolerance value‚ and datum references. The FCF formally specifies the geometric tolerance requirements for a particular feature. The frame’s contents precisely define how the tolerance applies to the feature and how it relates to the established datums. Understanding the arrangement and meaning of symbols within the FCF is essential for accurately interpreting GD&T specifications. Proper interpretation ensures that the manufactured part meets the design intent. The proper use of datums and FCFs is crucial for effectively communicating and controlling the geometric characteristics of parts.
Rules and Principles of GD&T (Rule #1 and Rule #2)
GD&T’s fundamental rules ensure consistent interpretation and application of tolerances. Rule #1‚ the Envelope Principle‚ dictates that the form of a regular feature of size is controlled by its size limits. This means that any deviation from perfect form must fall within the overall size tolerance zone. It simplifies tolerance control by tying form to size‚ which is particularly relevant for features controlled by both size and form tolerances. Understanding Rule #1 is essential for ensuring that parts meet the specified size and form requirements and that the process is consistent. This rule reduces ambiguity and promotes efficient manufacturing processes.
Rule #2 clarifies the application of geometric tolerances relative to the feature’s size. Unless otherwise specified‚ all geometric tolerances apply regardless of feature size (RFS). This means that the tolerance zone is always established relative to the theoretical perfect geometry of the feature‚ irrespective of the actual size variation within the size tolerance. The application of RFS avoids potential ambiguity in tolerance interpretation‚ promoting clarity in manufacturing. It streamlines the manufacturing process by providing a clear and concise standard for tolerance application‚ regardless of feature size variation. The consistent application of Rule #2 enhances the clarity and efficiency of engineering drawings.
Practical Applications of GD&T Symbols
GD&T symbols are crucial in manufacturing processes‚ ensuring parts meet precise specifications. They improve communication between designers and manufacturers‚ reducing errors and improving product quality and reliability. Proper implementation of GD&T streamlines manufacturing and inspection.
Using GD&T in Manufacturing Processes
Integrating GD&T into manufacturing workflows significantly enhances precision and efficiency. By clearly defining acceptable variations in dimensions and geometric features‚ GD&T minimizes ambiguity and ensures consistent part production. This leads to reduced scrap rates‚ improved quality control‚ and faster production cycles. Manufacturers utilize GD&T annotations on engineering drawings to guide machining‚ assembly‚ and inspection processes. The symbols provide a standardized language‚ eliminating misinterpretations and facilitating smoother collaboration across teams. Furthermore‚ GD&T promotes the use of advanced measuring equipment and techniques‚ enabling more accurate verification of part conformity. This proactive approach to dimensional control ultimately contributes to the creation of higher-quality products that meet or exceed customer expectations. The implementation of GD&T can be supported by readily available software and tools‚ including PDF viewers capable of accurately displaying and interpreting GD&T symbols. This accessibility simplifies the integration of GD&T into existing manufacturing processes‚ making it a valuable asset for companies of all sizes. Adoption of GD&T results in improved overall manufacturing performance and cost-effectiveness.
Leave a Reply
You must be logged in to post a comment.